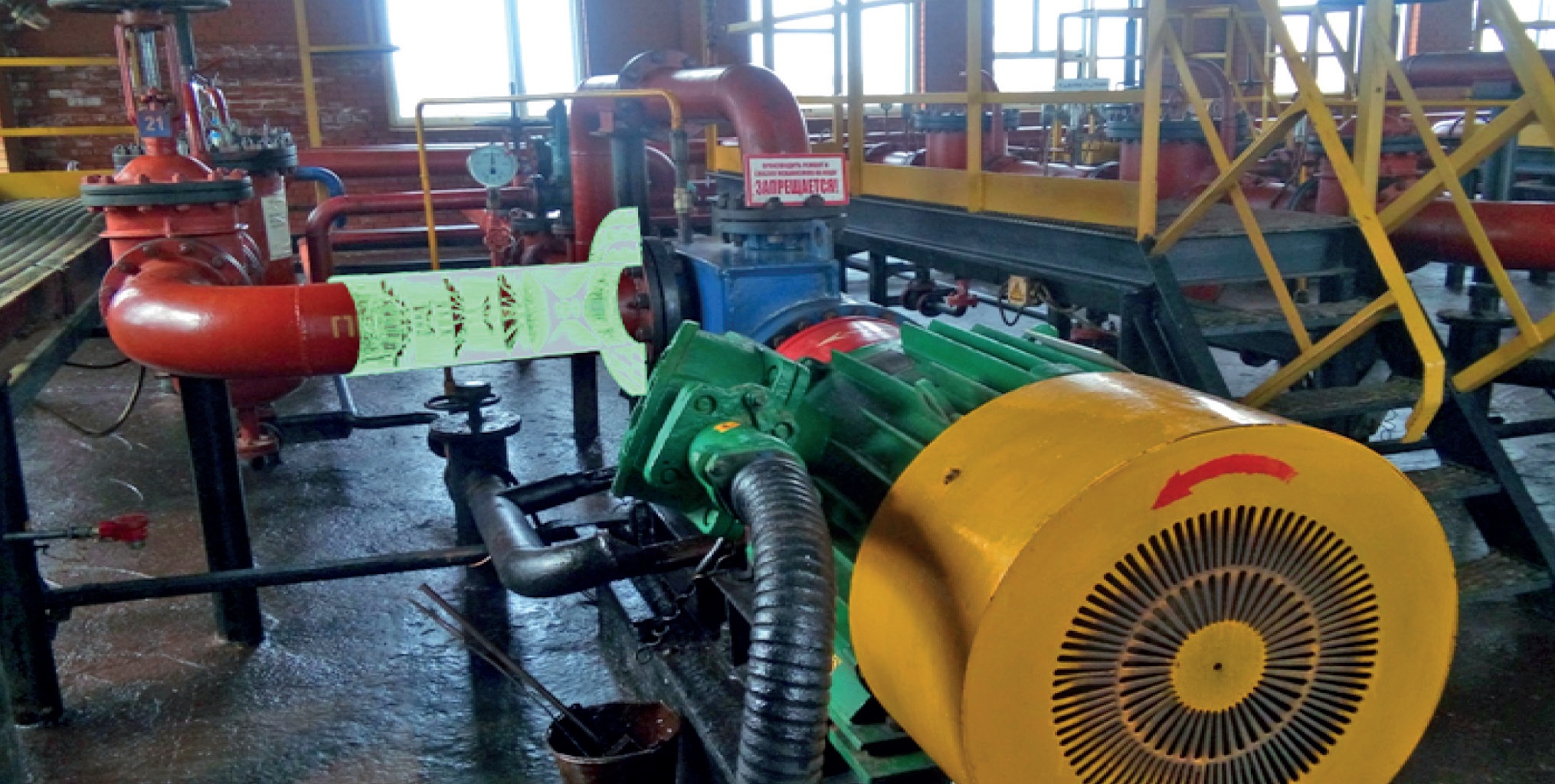
В статье представлен метод оптимизации технологии промыслового сбора попутного нефтяного газа на месторождениях ООО «Башнефть-Добыча». Транспортировка газожидкостной смеси в рамках применения данной технологии осуществляется с помощью мультифазных насосов по трубопроводной сети от пункта сбора до пункта подготовки
нефти, газа и воды в отсутствие отдельных газопроводов. В рамках обзора рассмотрены особенности эксплуатируемых месторождений, в частности Арланского, оказывающие влияние на применение мультифазных насосных станций. Показано, что определенные трудности при эксплуатации связаны с образованием газовых скоплений в
промысловых трубопроводах.
Вариант оптимизации работы мультифазной насосной станции заключается в применении диспергатора RCM-04 – набора радиально-коаксиальных камер (обратных конусов с кавитационными бортиками). Описаны принцип действия и способ монтажа устройства смешения газожидкостных смесей. Обоснован расчетный базис, приведен
поэтапный порядок проектирования диспергатора. Проанализированы возможные варианты конструкции, перспективы оптимизации технологии, эксплуатационные ограничения и трудности, которые могут оказать влияние на процесс внедрения.
Представлены результаты опытно-промышленного испытания, проведенного для оценки изменения степени дисперсности среды при использовании устройства смешения RCM-04: 1-й этап – без «газовой подушки», 2-й этап – с «газовой подушкой». Проанализированы параметры функционирования рабочих органов мультифазной насосной
станции, приемных, жидкостных и выкидных линий, общесборного коллектора при эксплуатации без смесительного устройства и после его установки.
Для организации промыслового сбора попутного нефтяного газа на месторождениях ООО «Башнефть-Добыча» широко применяются мультифазные насосы. Данная технология позволяет транспортировать газожидкостную смесь по существующей трубопроводной сети от пункта сбора до пункта подготовки нефти, воды и газа в отсутствие отдельных газопроводов. При этом отпадает необходимость применять газовые сепараторы на объектах сбора и сжигать попутный нефтяной газ в факелах.
В 2003 г. на Арланском месторождении Нефтегазодобывающего управления (НГДУ) «Арланнефть» была введена в эксплуатацию первая мультифазная насосная станция ОАО «Ливгидромаш», представленная двумя двухвинтовыми эксцентрико-шнековыми насосами объемного действия А3 2ВВ 63/25-50/25-01, позволяющими перекачивать газожидкостную смесь за счет образования полостей между ротороми статором. Насосы оборудованы частотным приводом и автоматической системой управления, позволяющими контролировать скорость вращения шнеков в зависимости от объемов перекачиваемой смеси, температуру узлов, давление на приеме, температуру перекачиваемой эмульсии и ряд других показателей.
В настоящее время в ООО «Башнефть-Добыча» мультифазная технология перекачки газожидкостной смеси внедрена на пяти объектах подготовки и перекачки нефти, газа, воды. Текущий объем транспортируемой газожидкостной смеси составляет 25 тыс. м3/сут, в перспективе, после ввода мультифазной технологии еще на трех объектах подготовки нефти, газа и воды, данный показатель достигнет 55 тыс. м3/сут.
Наряду с явными преимуществами применение мультифазной технологии сопровождается эксплуатационными ограничениями, обусловленными изменяющимися условиями режима течения газожидкостной смеси и загрузки насосных агрегатов. С момента ввода мультифазной насосной станции в эксплуатацию изменились объем и состав транспортируемой среды. На Арланском месторождении вследствие разбуривания глубоко залегающих продуктивных горизонтов увеличивается количество добываемой нефти, характеризующейся высоким газовым фактором. В результате зафиксировано повышение газового фактора по отдельным скважинам (рис. 1).
Учитывая, что основная часть месторождений ООО «Башнефть-Добыча» расположена в условиях сложного пересеченного рельефа местности, применение мультифазной технологии сопровождается дополнительными трудностями при эксплуатации, связанными с образованием газовых скоплений в промысловых трубопроводах, сопровождающимся:
• пульсацией давлений и расхода в периоды миграции крупных пузырей;
• уменьшением амплитуды гидравлического удара;
• срывом в работе насоса при прохождении газовой пробки через его проточную часть.
Как следствие, эксплуатация данных насосов на неоптимальных режимах, оборотах, с пульсацией на входе в насос и неравномерной подачей газожидкостной смеси приводит к чрезмерному повышению температуры агрегата, возникающему при длительном прохождении газовой пробки. При этом срабатывает система защиты агрегата, и насос останавливается. Применение данной технологии создает риски в части надежности эксплуатации объектов перекачки и подготовки нефти и газа.
Производителями насосного оборудования предлагались такие решения по стабилизации потока, как:
• монтаж емкостей для периодической дозировки жидкости;
• организация особых условий обвязки приемной и выкидной линий;
• устройства для снижения пульсации при транспорте газожидкостной смеси по рельефной местности и т. д.
Однако анализ показал, что все предложенные решения требовали дополнительных капитальных вложений. В статье рассмотрен вариант оптимизации работы мультифазной насосной станции (МНС) с применением диспергатора RCM-04, представляющего собой набор радиально-коаксиальных камер.
ОПИСАНИЕ ТЕХНОЛОГИИ ОПТИМИЗАЦИИ РАБОТЫ МУЛЬТИФАЗНОЙ НАСОСНОЙ СТАНЦИИ С ПОМОЩЬЮ ДИСПЕРГАТОРА RCM-04
По результатам анализа фактических параметров эксплуатации наземной инфраструктуры Арланского нефтяного месторождения была выделена наиболее проблемная мультифазная насосная станция н
а установке предварительного сброса попутно добываемой воды № 1 (УПС-1) производства ОАО «Ливгидромаш». Данная мультифазная насосная станция предназначена для обеспечения перекачки газожидкостной смеси с трубного водоотделителя 1 (ТВО-1) на установку комплексной подготовки нефти (УКПН). На ТВО-1 предусматриваются разгазирование нефти и сброс пластовой воды.
В описываемом случае в результате анализа работы мультифазной насосной станции на УПС-1 с насосными агрегатами марки 2ВВ А3 63/25 У2 была подобрана конструкция с тремя камерами смешения.
Устройство монтируется непосредственно на приемной линии, подводящей сырье к насосу или аппарату, в котором необходимо создать устойчивую газожидкостную среду. Диспергирование происходит за счет последовательного прохождения потока через радиально-коаксиальные камеры,
а затем через сопло Лаваля. При прохождении потока через сопло Лаваля происходит мгновенное растворение газа в жидкости, связанное с повышением давления. Радиально-коаксиальные камеры представляют собой обратные конусы с кавитационными бортиками, рассчитанные таким образом, что часть энергии потока эффективно, без «паразитных» потерь, переходит в работу по диспергированию, причем каждая следующая камера уменьшает размер глобул, позволяет достичь более равномерного распределения и подготавливает поток газожидкостной смеси» для прохождения через сопло Лаваля, в котором за счет разности давлений создается устойчивая газожидкостная эмульсия. Количество радиально-коаксиальных камер может быть увеличено до пяти, в зависимости от физико-химических свойств перекачиваемого состава. Внутреннее устройство RCM-04 является разборным, что позволяет при необходимости проводить демонтаж, ревизию, очистку и замену внутренних смесительных элементов. Гидравлическое сопротивление устройства обычно составляет 0,1–1,0 атм, но не более 10 % от начального давления.
Принцип действия в общем виде заключается в следующем:
1) газожидкостная смесь входит в приемный патрубок смесителя и проходит первую радиально-коаксиальную камеру, в которой происходит равномерное распределение газа в жидкости по всему объему;
2) поток проходит через вторую радиально-коаксиальную камеру, в которой происходит образование более мелких глобул газа в жидкости;
3) третья радиально-коаксиальная камера позволяет достичь максимального распределения газа в жидкости;
4) газожидкостная смесь проходит через сопло Лаваля, где газ мгновенно растворяется и далее, на выходе из сопла, испаряется в жидкости.
В результате повышается дисперсность среды и создается стабильная газожидкостная эмульсия, поступающая на подающий винт насосного агрегата.
Полученная мелкодисперсная система «газ – жидкость» даже при малом содержании жидкости способствует
охлаждению насосного оборудования в связи с гомогенностью среды.
На рис. 2 изображен способ монтажа смесительного устройства RCM-04 в трубопроводе линии подачи насоса.
ПОСТРОЕНИЕ МАТЕМАТИЧЕСКОЙ МОДЕЛИ ПРОЦЕССА СМЕШЕНИЯ В РЕЖИМЕ С ИСПОЛЬЗОВАНИЕМ ДИСПЕРГАТОРА RCM-04
Специалистами ООО «Хаммель» произведена обработка исходных данных с выбранного объекта, построена математическая модель процесса смешения, основанная на авторских методиках разработчиков устройства. Расчет основан на выборе соотношений скоростей по этапам смешения, а также на экспериментальных данных, полученных в результате исследования смесей с различным соотношением газа и жидкости. Далее представлен подход к расчету гидродинамики смесительного устройства.
Основным фактором, влияющим на конструкцию проектируемого устройства, является соотношение газа и жидкости в планируемой точке смешения при планируемых параметрах (Р, Т). На рис. 3 представлена упрощенная схема течения газожидкостной системы в трубопроводе. Как известно из теории истечения, газ концентрируется в центре трубопровода, а жидкость – у периферии. Это связано с различием сил трения между трубопроводом/газом/жидкостью, а также с разностью плотностей сред. На первом этапе проектирования рассчитывается диаметр основания «конуса износа», как указано на рис. 3.
Устройство RCM-04 может иметь несколько ступеней радиально-коаксиального смешения, однако первая ступень служит не для получения высокодисперсных смесей, а для нарушения классического истечения газожидкостных смесей вдоль трубопровода круглого сечения.
Дальнейший расчет устройства заключается в определении требуемого количества энергии, необходимого для диспергирования газовой среды в жидкости (в некоторых случаях – наоборот). Расчет основан на теории взаимной растворимости, разделении газовой и жидкостной части на составляющие, различающиеся по нескольким ключевым параметрам (давление насыщенных паров, температура кипения, вязкость, плотность, растворимость и летучесть). В рамках данной статьи приведение вышеупомянутого расчета нецелесообразно в связи с большим его объемом. Результатом расчета требуемой работы по диспергированию является количество энергии Атр (в кДж), необходимое для получения дисперсной системы заданного качества.
Третьим этапом задачи является расчет конструкции радиально-коаксиальных камер, позволяющий перевести энергию движения потока, равную Атр/коэффициент полезного действия, в энергию диспергирования. Исходя из стендовых и промышленных испытаний, коэффициент полезного действия (КПД) устройства RCM-04 достаточно велик
и достигает 0,85–0,92.
На рис. 4 представлена база для расчетного алгоритма второй и последующих камер радиально-коаксиального смешения устройства RCM-04. Задача решается с использованием векторных уравнений и уравнений гидравлики. При столкновении с малым конусом происходит процесс, аналогичный стандартному «внезапному повороту потока». Такое местное сопротивление,называемое коленом, сильно влияет на потери напора. В нем происходит отрыв потока от стенок конструкции и создаются сложные вихревые зоны в которых энергия потока оказывает интенсивное турбулентное воздействие на среду. Степень интенсивности существенно зависит от угла поворота N2.
Коэффициент местного сопротивления возрастает с увеличением угла поворота, и его можно определить по формуле:
. (1)
На рис. 4 обозначены рабочие зоны диспергирования – зона механического соударения потоков за счет направляющих конусов и зона кавитации (пульсации давления). В обеих этих зонах происходит переход энергии потока в работу по диспергированию. Потери давления на малом конусе составят (модифицированное у
равнение Дарси – Вейсбаха):, (2)
где l – длина пути; u – средняя скорость;
D – переменный диаметр условного прохода (от диаметра трубы до условного диаметра сечения конуса).
Аналогично уравнению (2) решается задача и с большим конусом. При расчете всех участков устройства используются критерии подобия и коэффициенты корреляции, полученные при проведении стендовых испытаний. Строится модель из необходимого количества радиально-коаксиальных камер с необходимым «углом атаки» конусов.
На рис. 5 представлена схема сопла Лаваля с условными размерами. Расчет данного устройства производится по классическим методикам и не имеет никаких особенностей. Результатом расчета является потеря давления на данном аппарате при условии соблюдения исходных данных – давление в зоне критического сечения позволяет растворить 40–55 % газов.
Для определения работы по диспергированию используем следующее уравнение:
дисп = E1 – E2, (3)
где E1, E2 – энергии потока до и после устройства;
Ei = PidS.udt, (4)
где Pi – давление в i-й точке системы;
S – площадь сечения условная; u – средняя скорость потока на участке i;
t – время прохождения участка.
Определенная работа по диспергированию сравнивается с рассчитанной ранее AТР , при необходимости производится перерасчет устройства для достижения значений:
0,99.AТР < AдиспКПД < 1,10AТР.
РЕЗУЛЬТАТЫ ОПЫТНО- ПРОМЫШЛЕННОГО ИСПЫТАНИЯ
В рамках опытно-промышленного испытания (ОПИ) для оценки изменения степени дисперсности среды проанализированы параметры функционирования рабочих органов МНС, приемных, жидкостных и выкидных линий, общесборного коллектора при эксплуатации бе
з смесительного устройства и после его установки. ОПИ проводилось в два этапа:
1-й этап – в текущем режиме работы ТВО-1 (без «газовой подушки») в течение 8 дней;
2-й этап – в режиме работы ТВО-1 «по уровню» (с «газовой подушкой»), экспериментально в течение 1 дня.
На рис. 6 видно, что установка смесительного устройства на приеме насоса существенно повлияла на изменение спектра «звуч
ания» и на его интенсивность при разных частотах. Согласно исследованиям Б.В. Бошенятова в области
гидродинамики микропузырьковых газожидкостных сред [1–3] изменение амплитуды колебаний свидетельствует об изменении степени дисперсности среды и равномерности распределения пузырьков газа в объеме жидкости. Кроме того, спектр «звучания» свидетельствует об общем снижении уровня шума в период работы насосного агрегата.
На рис. 6 также показаны результаты измерения спектров «звучания» и их интенсивность при разных частотах, а также сравнение с результатами исследования, полученными на первом и втором этапах. При работе в режиме «с газовой подушкой» были зафиксированы периодические всплески колебаний
высокой интенсивности, что свидетельствует о периодическом поступлении порций газа из газовой подушки. Следует отметить, что данное явление не ухудшило эксплуатационные характеристики насоса и не привело к нарушениям температурных режимов его работы.
Произведена оценка динамики изменения температуры подшипника со стороны редуктора при эксплуатации без смесительного устройства и после его установки. Зафиксировано снижение температуры подшипника при эксплуатации со смесительным устройством RCM-04, свидетельствующее о постоянном поступлении гомогенной жидкой среды либо жидкой среды с равномерно распределенными в ней пузырьками газа.
ЗАКЛЮЧЕНИЕ
1. Устройство RCM-04 обеспечило стабильную работу мультифазных насосных станций.
2. Восполнена нехватка номинальных мощностей мультифазных насосных станций для организации откачки газожидкостной смеси с учетом увеличения уровня добычи.
3. Предлагаемая технология предоставляет возможность отказаться от необходимости технического перевооружения объекта, требующего дополнительных капитальных и эксплуатационных затрат.
4. Установлено, что применение устройства RCM-04 позволяет расширить область применения мультифазных насосных станций в условиях изменения соотношения газа и жидкости в перекачиваемой среде.
А.Ф. Садыков, Д.А. Гарипов, А.С. Кондратьев, С.А. Нонява
Литература:
1. Струминский В.В. Микропузырьковая газожидкостная среда // Доклады Академии наук СССР. 1990. Т. 310. № 6. С. 1323–1326.
2. Бошенятов Б.В. Исследование течений микропузырьковых газожидкостных сред в гладких трубах // Известия Томского политех. ун-та. 2005.
Т. 308. № 6. С. 161–164.
3. Чернышев И.В. Экспериментальное и теоретическое исследование гидродинамики микропузырьковой среды: автореф. дис. … канд. физ.-мат.
наук. М., 1989. 12 с.